Industrial food manufacturers are known to use an incredible amount of energy when it comes to operating their facilities. Whether it is electric or thermal energy , food manufacturers depend on having enough precisely when they need it in order to operate smoothly. This need for a large amount of energy comes at both a great financial and emissions cost.
For that exact reason, major food manufacturers across the country are always looking for new and meaningful ways to either decrease their energy needs – or rather, make their energy usage more efficient – so that they can optimize the energy dollars spent and improve the bottom line.
That is why many food manufacturers evaluate and implement combined heat and power (CHP), also known as cogeneration. Adding a CHP system to a food processor facility is one of the best ways to take advantage of top technologies in order to see a business prosper.
How it Works
Overview of Benefits
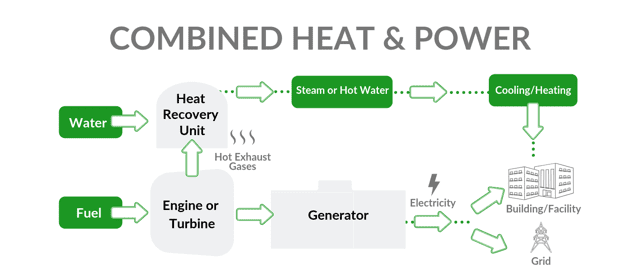